Coal Mining in Cape Breton
I grew up reading 'Sydney' on
the rails of the nearby CNR railway ... and 'Algoma' on the rails of
the CPR. In 1990 at Coldwell, Ontario, it read 'Nippon' on the rails
which the CPR was about to install.
In 1980 and 1988, during vacations to the Atlantic Provinces, the
unique industrial heritage of Cape Breton around Sydney provided an
interesting lesson in Canadian history for us. This page is an attempt
to explain some aspects of the pursuit of this ancient mineral resource
from the beginning.
This page has become so large,
that I have attempted to lessen the misery of visitors by adding the
table of contents below, with links back and forth within the page.
Most readers will probably be content to simply have a quick look at the sections which interest them.
Introduction
Early collieries in Britain
Mine ventilation
A Canadian steam powered colliery railway in the 1830s
George Monro Grant describes Cape Breton in 1882
Happy Mine
Cornish pumping engine
Engineering, Scottie here.
Coal near Sydney
Get the most from your mine!
Boys in the mines
Endless rope haulage & Tippler work
Technology in Nova Scotia mines
Some uses of coal in the early 1900s
Glace Bay
Introduction
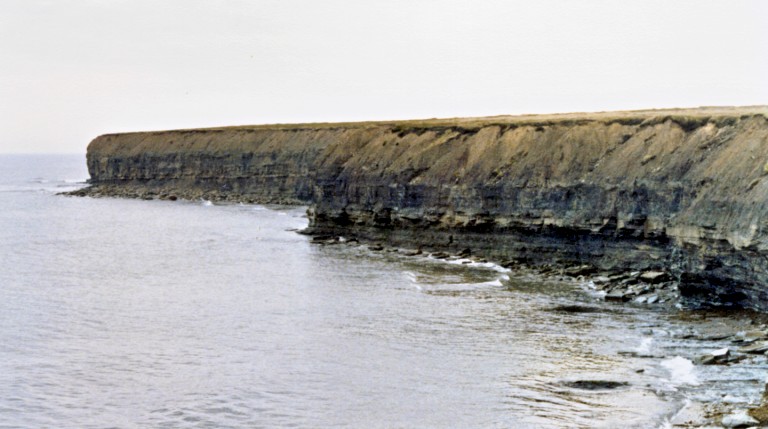
The seashore at Glace Bay, Cape Breton, Nova Scotia in 1980.
One of Canada's few areas of 'coal measures' ... seen during a vacation trip.
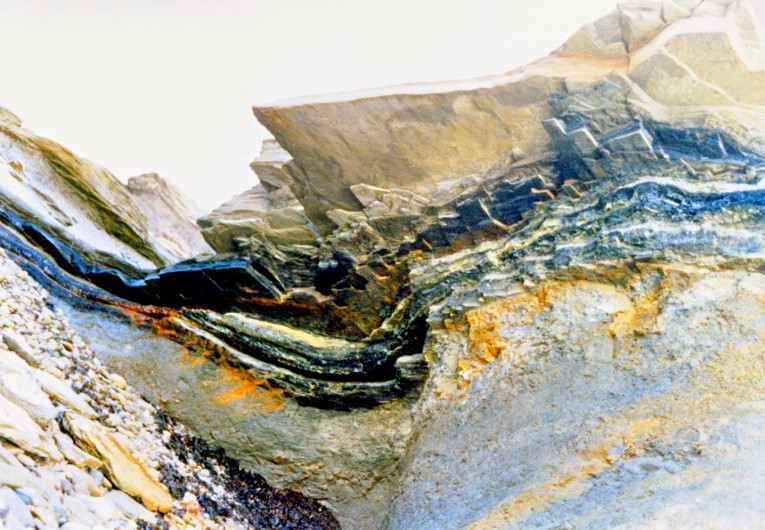
Looking up from the same shoreline to representative sedimentary rocks containing a little iron and a little coal.
Coal is not a uniform substance of uniform quality for burning ... unlike ... a manufactured 'sawdust log'.
A great deal of practical experience and 'nature study' over time was necessary
to understand how to effectively exploit this natural resource.
Coal was essential in creating the 'western civilization' which many of us inherited ...
It reminds us of other climates and now obsolete life forms which were here long before us.
If history is any guide ...
The geological record of coal will exist long after the planet bids our civilization farewell.
* * *
Often shale is found just above
coal. Layers of clay are often found just below coal seams.
When ancient people (like the original 'Britons') burned coal it was often found as sea coal ...
which had been released by the power of the waves from the shore ... 'hey, this black rock burns!'
People also found this mysterious rock in simple surface
outcroppings. Hacking away at the outcroppings they would 'mine' as
much as they could.
Shapes in the coal looked like plants people had never seen before
... they gradually developed theories about where coal came from.
Much
more important than 'theories' to utilitarian people concerned about comfort or trade was ... where could more of this really
excellent fuel be found ... should they look for other 'plant picture
rocks'? Could coal be found everywhere (in Britain) just be digging deep
enough?
To spoil the surprise ... coal was formed during the
Carbon-iferous period roughly 360 to 300 million years ago. Massive amounts of
plant material with lots of lignin (lignin is barky stuff) died and
fell down.
One explanation for coal's subsequent formation is that nothing had evolved to digest all this
lignin so it was very well preserved - just like Dick Clark.
This is what is so special and precious about coal ... it is
sedimentary or metamorphic rock made out of STP - Specially Treated
PlantMaterial.
It has lots of 'big carbon' molecules which had no
useful purpose in life ... until we thoughtfully came along and started
pyrolyzing and oxidizing them ... i.e. turning rocks into air.
One aspect of atmospheric science linked to this Carbonosaurus
Period is that with all this lignin going
into proto-coal carbon-sinks ... the atmosphere had 'too much' oxygen
in it. Without even doing cardio twice a week ... super-sized,
inefficient animals could thump around the planet without even getting
winded!
Those were the Good Old Days.
Back to Top
Early Collieries in Britain
So coal is laid down in layers like other sedimentary rocks ... but
unlike the particles forming shale (clay) or sandstone ( ... sand! ... geez!) ... coal is made of old plant material which
has received some kind of protection from being completely broken down
by micro-organisms and weathering. Maybe the decaying swamp was acidic ... maybe not
enough 'bugs' could digest it at that time in geological history ... maybe it was effectively sealed away
under other sediments. Some kinds of coal (e.g. anthracite coal) is more
accurately a 'metamorphic rock' as its original sedimentary
characteristics have been altered by great heat and/or great pressure.
As society demanded more and more coal, British miners devised all sorts of techniques and technologies to obtain it. As
a layer of rock lies around for 300 million years, it is subject to all
the effects of plate tectonics ... and forces above the
lithosphere such as weathering, glaciation, and flooding.
Much of the 'coal measures' in Britain had been subject to
all sorts of scrunching by tectonic plates coming together. So instead
of a nice flat thick bed of coal like a pan of brownies ... British coal miners
often found irregular coal beds sloping almost vertically ... or
discontinuous faulted beds with some sections up and some sections down ... or
folded coal seams which took on shapes like the letter 'W'.
Early coal pits were simply ...
pits. They took the shape of bells as the important coal layer at the bottom was
harvested down and out to the point of causing the walls of the pit to collapse.
There was a general expectation by property owners that the previous bell pit would be
filled in by the miners before starting the next.
Then the pits began to evolve into 'mines' as we know them ... a single shaft
was
dug to reach the level of the coal deposit and tunnels were picked and
shovelled ... radiating from this subterranean base to obtain as much
coal as possible from the single deep shaft. Woven baskets, wheeled
vehicles, and eventually
vehicles travelling on rails, were used to slide the coal back to the
vertical pit. Back at the pit or shaft ... ladders were used by workers to
carry baskets of
coal to the surface.
Eventually tubs ... hoisted by ropes ... which ran
through pithead or 'headframe' pulleys ... were hauled up by horses working on the surface.
The definition of 'horsepower' (550 foot-pounds per second) as applied to engines or motors, is
derived from horses lifting coal out of the pits ...
Miners wanted to know ... to dead-lift people, water, and coal straight up
mineshafts ... could a particular steam engine provide the performance
they required?
from The History and Description of Fossil Fuel, circa 1850
'Children
began their life in the coal mines at five, six or seven years of age.
Girls and women worked like boys and men, they were less than half
clothed, and worked alongside of men who were stark naked. There were
from twelve to fourteen working hours in the twenty-four, and these
were often at night. Little girls of six or eight years of age made ten
to twelve trips a day up steep ladders to the surface, carrying half a
hundred weight of coal in wooden buckets on their backs at each
journey. Young women appeared before the commissioners [investigating
mine conditions in Britain], when summoned from their work, dressed
merely in a pair of trousers, dripping wet from the water of the mine,
and already weary with the labor of a day scarcely more than begun. A
common form of labor consisted of drawing on hands and knees over the
inequalities of a passageway not more than two feet or twenty-eight
inches high a car or tub filled with three or four hundred weight of
coal, attached by a chain and hook to a leather band around the waist.'
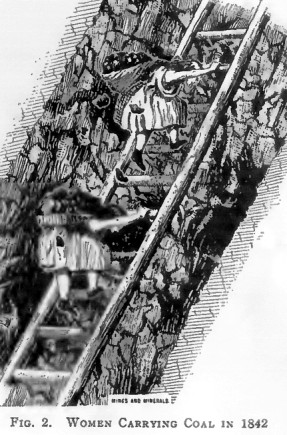
Legislation was passed in Britain in 1842
prohibiting women and boys under thirteen years of age from working in
mines ... as well as regulations for lighting, hours of work,
ventilation, safety, and licensing of engineers. There were still
plenty of things which would continue to threaten human life
underground throughout the history of coal mining ...
- Sometimes, in the small, cramped mining chambers, a miner
would unexpectedly trigger a massive ceiling collapse which would kill
him.
- An adjacent pocket of water or an underground watercourse could suddenly fill the lower works, drowning the miners.
- Originally, sudden deaths without visible physical trauma
were thought to be caused by evil spirits or goblins. Later they were
categorized by descriptive terms which were retained even after the
chemistry behind the deaths was finally understood ...
- Explosions
were caused by 'Fire Damp' - methane ('light carburetted hydrogen') often mixed with suspended coal dust.
- Suffocations were caused by 'Black Damp' or 'Choke Damp' ... gases such as carbon dioxide ('carbonic acid gas').
- Suffocations could also be caused by 'After Damp' ... which followed a 'Fire Damp' explosion which had used up the oxygen.
Using whale oil lamps usually attached to their clothing as they travelled, miners used
picks, shovels and wedges to break the rock and coal into manageable
pieces. Blasting powder was also used with a powder-filled
straw serving as a fuse.
Clearing accumulated water seepage from the mines was such a persistent
and universal problem that it led to the invention of the first
(atmospheric) steam engines.
An early reversible mineshaft hoisting device circa 1840
A mine headframe and pulley ... are located at 'A'.
The hoisting rope is taken up on the reel at 'B'.
A horse operating the windlass (or 'gin') is at 'C'.
To lower items or miners, the horse would be reversed and walked in a clockwise direction.
Newcastle-upon-Tyne in 1783 - an important coal centre dating back to the 1400s.
Before the Industrial Revolution
employed steam power, various railway technologies were already being
used to increase efficiency. Usually, the mission was to get coal from
a mine ... to a canal or sea transport at a lower elevation. At water
level, sailing ships or common coal barges ('keels') would be used for
transportation. The coastal shipping of coal provided basic training for many
sailors who would go on to crew British warships or merchant vessels on
the high seas - sometimes, whether they wanted to or not (when the Press Gangs were in town).
The design of the coal wagon above (like the keel barges) was
generally a
standard design which evolved slowly. Copies of traditional coal wagons
like this are also shown in some early coal mining photos
from Nova Scotia. Many miners and mining engineers came to Cape Breton
from Britain ... and brought their usual technologies with them. Above,
putting the cart before the horse, the driver is SITTING on the
mechanical brake lever (called a convoy)
to control speed down the grade as he smokes his pipe. On
steeper parts of the run downhill, the horse can provide additional
braking force ... the driver hopes. The brake can also overheat -
sometimes setting the wooden cart on fire. Beyond the bridge, you can see a
keel or two on the river.
The 'staith' illustration above
shows
features which allow the specialized coal pier to load both sailing
ships and keels. The chute
above 'L' could be used to load the low-slung keels if a mine wagon was
emptied above the letter 'G' - 'L' is a 'trunk staith' . A loaded wagon
weighed 2
to 3 tons. "When a waggon lets fall its contents down one of these
spouts, the noise at a distance very much resembles a clap of thunder".
This kind of rough treatment would be unacceptable for the lowest
quality
coals, as they would turn into unmarketable dust.
To load the sailing ship, the loaded wagon in the cradle at ' I ' ...
is lowered in an arc from the pier's cabin ... by the
boom 'D'. To maintain control,
the staith operator brakes the reel hidden from us inside the cabin ... which
spools
the ropes 'C' as the heavy wagon descends over the sailing
ship's hold. Often a staith labourer would ride down with the cradle
and coal wagon, tripping the wagon's trap door and releasing the coal into the ship's hold.
Unloaded, the coal wagon is lighter ... and the attached counter-weight
of cast iron plates 'H' raises the boom and the empty wagon to their starting position.
In the 1840 'horse gin' hoist illustration above, a pit with a vertical shaft was depicted.
As this 1880s textbook suggests, many additional techniques had been worked out to tunnel out coal however it lay.
After the bell pit design was abandoned,
a coal mine became a complex piece of architecture
...
with multiple systems engineered and installed to protect life and efficiently
remove as much coal as possible.
Furthermore, a mine was only 'complete' once further architectural change yielded no further financial reward.
As architecture, a coal mine provided the 'ultimate perpetual renovation project'.
Back to Top
Mine Ventilation
Out of necessity, mine
ventilation rapidly became quite a science.
Imagine a simple groundhog burrow with 'a means of egress' at each end ...
If one has access to the atmosphere at
each end of a tunnel ... simply
pushing or pulling the air through the
tunnel at one end would be adequate for good ventilation. The air will
take the shortest course to equalize its pressure.
... so a healthy and
efficient groundhog (probably after an engineering consultation with a
beaver) would erect an air scoop on the windward entrance of
the burrow to funnel the wind through.
Coal mines are irregular as their tunnels follow the usually disrupted pattern
of the coal bed. Ideally, miners dig out only coal as they tunnel ... with a natural 'ceiling' and 'pavement' of 'worthless' rock strata left undisturbed.
The luxury of an opening on each end is not possible
if the pit is very deep (e.g. Springhill, Nova Scotia) or the pit follows
the coal seam out under the sea (e.g. Sydney and Glace Bay, Nova Scotia).
Coal mine ventilation is like a maze puzzle which can be solved with
a pencil ... once the walls and baffles are put in place.
In the 1850s model mine pictured below - the ventilation system is is powered by two coal furnaces - the two grey rectangles on either side of 'x'.
"The furnace resembles an ordinary
old-fashioned fire-place with stout grate bars. It is constructed near
the foot of an opening into the mine, and furnished with a smoke-flue
built of brick. This flue leads into the air passage of the surface
opening at some distance above the floor of the mine. The volume of
heat from this furnace passing into the airway creates and maintains a
strong upward air current. In some mines the furnace is built at the
foot of an air shaft a long distance from the main opening, thus making
it an upcast air shaft. By the continued use of a huge fire in this
furnace a powerful current of air may be put and continued in motion,
but it is found an expensive way of 'raising the wind' and the system is
rapidly giving place to the rotary steam fan."
'The Springhill Colliery Disaster', 1891
Diagram, ventilation model circa 1850.
A Canadian steam powered colliery railway in the 1830s.
The 'Samson' in Nova Scotia.
The man between the chairs may have been George Davidson - the Scottish engineer
sent to Canada to assemble and manage the steam equipment at this location.
Albion (now known as Stellarton)
Nova Scotia was the site of the General Mining Association's coal
mining operations. Beginning in 1829, horses were used on a light
railway to draw coal cars out of the mines and to the wharf near
Pictou. The GMA had a legal monopoly which was significant in later
history as Nova Scotia and Canada became locally governed and sought local control over resources within their boundaries.
To pay a bill:
King George IV's brother - the Duke of York - was
granted the mineral rights to Nova Scotia and Cape Breton. The
Duke immediately paid a jeweller's debt with them and the rights were
subsequently purchased by a group of London investors ... naming themselves the
GMA.
Being a British syndicate, the GMA imported modern
industrial technology in the form of the locomotive 'Samson' and two
others. They were shipped from the coal centre Newcastle, England in
1838. The powerful ... for their time ... locomotives could pull about 100 tons, and weighed
about 20 tons themselves. You'll notice the unusual design - compared to more recent locomotives ... the
engineer and pistons are at one end ... and the firemen stokes from the
opposite end below the smokestack. I have always wondered if the
'ergonomic' seats for the engineer were securely anchored. Today the
locomotive 'Samson' is preserved at Stellarton.
Smelting iron from the nearby mine, 3 foot cast iron 'fish belly' rails were
made for the railway ... some wavy fish belly rails can be seen in the centre foreground.
We may think of modern railways as intercity 'common carriers' moving
anything or anyone who wants to travel. Back in the Samson era, the
coal mining industry of Britain was a major employer of short private horse
tramways and steam powered railways to get coal from the mines
to the nearest water transportation. This pattern was also common around
Nova Scotia's coal and iron operations. Passenger transportation, in
the form of stage coach bodies mounted on flanged wheels, was
an afterthought.
Back to Top 
George Monro Grant describes Cape Breton in 1882
"The harbour of Sydney, sheltered, commodious, and of easy access, is of
no mean maritime value. During the season of navigation steamers on the
voyage to Europe from the more southern ports of the United States,
and from the St. Lawrence, call for bunker coals and lie clustered
about the colliery wharves which railroads connect with the mines in
the interior. With these are some of the many steamers engaged in
carrying coal to Montreal, and humbler craft which supply the nearer
and less important markets. The mine on the shores of Sydney harbour
has great advantages over the exposed outports in which vessels take in
cargo. Many fishing and trading schooners lie off the new and more
active town of North Sydney, while the frequent visits of French and
British men-of-war give dignity to the older town.
"The harbour divides into two great arms, and on a peninsula which marks
the entrance to the Southwest arm stands the town of Sydney, which was,
before the union of Cape Breton and Nova Scotia, the seat of
government. At the end of the peninsula are the remains of earthworks
and dilapidated and dreary quarters for the garrison which was
stationed here until the Crimean War. Other traces of departed glories
are to be found only in the traditions of the inhabitants. Their
splendours have not taken more concrete shape.
" ... But Sydney at an earlier day than that of its possession by the
British has seen stirring scenes. French and British fleets have made
its harbour a rendezvous, not, as now, in peace, but as a point of
vantage in their struggle for the continent. ... The old name of
Sydney, Spaniards Bay, came from a time when, although the fishing
grounds were neutral, fishermen of different nationalities resorted to
different harbours, so that the occasions of rekindling in the New
World the animosities which made Europe a battlefield might, as much as
possible, be avoided. The Spaniards came then to Sydney, the French to
St. Anne, while English Port, the name of Louisburg before it became a
French stronghold, shows that it had been the chosen resort of English
fishermen. None of these nations laid claim to the island; there were
no laws, and justice depended on a consensus of opinion among enough
captains of vessels able to enforce it ...
Not in 'Happy Mine'
From a British coal mining textbook (1880s)
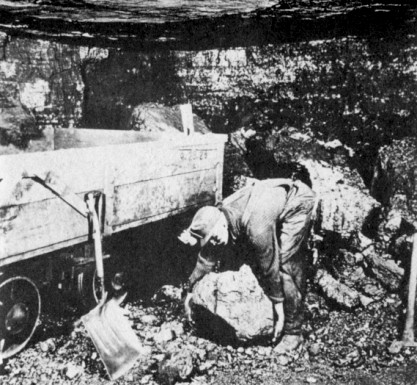
At the coal face, loading a car.
Immediately above and below from:
"The Company Store
J.B. McLachlan and the Cape Breton Coal Miners 1900-1925"
John Mellor, 1983.
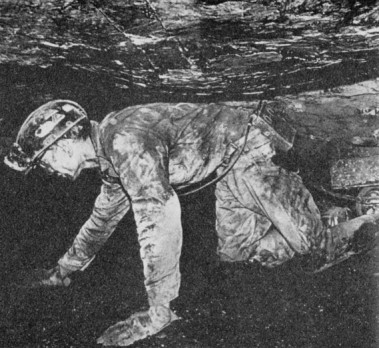
Modern generic photo of a miner in a 3 foot seam.
In the 1920s, miners being punished by the company sometimes worked these seams.
It was not possible to meet the normal daily pay expectation (based on tonnage) working under these conditions.
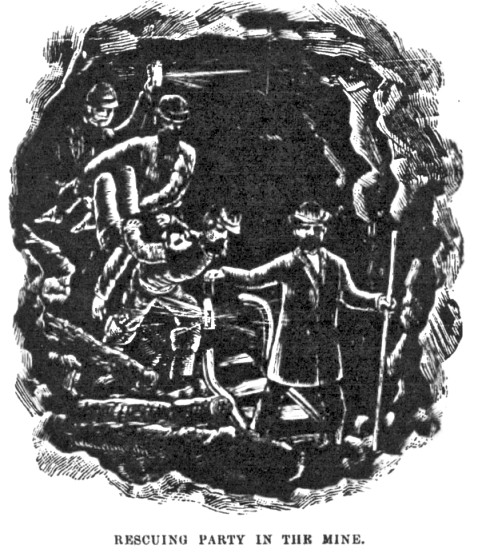
Springhill 1891 - 125 miners killed in an explosion.
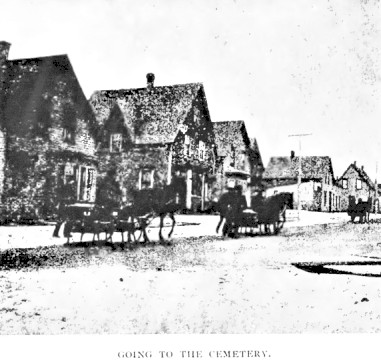
Springhill 1891
Back to Top 
The Cornish Pumping Engine
Cornwall, at the extreme
southwest corner of England, was known for its tin and copper mines for
centuries. Given this long history, we can assume the metals were near
the surface and could be obtained with hand tools.
Another important factor was that these, and early coal mines as well,
could be drained by 'adits' ... a traditional term for 'gravity mine
drain'.
In other words ... water in the mine had somewhere 'down' it could flow
so it was worthwhile to dig a little sloping tunnel to the outside to get rid of it
... problem solved.
Once the easy high and dry mining was finished in the region, people carried the
water out, or horses powered 'winding engines' to lift the water out in containers.
The first 'atmospheric' steam engine of Newcomen design was used in 1712.
If you care: ... atmospheric engines work sort of like this ... heat and fill a flexible plastic bottle (your 'piston') with steam from a kettle boiling over a coal fire
... screw the cap on the plastic bottle and remove it from the heat. As the air/vapour in the
bottle cools ... the pressure inside decreases ... and the bottle
eventually gets bent out of shape by atmospheric pressure. So 'work' is
done only when all the heat energy is completely thrown away. This was a great technological advance at the time, but it burned a lot of coal.
Thereafter, technology slowly shuffled along, until steam's expansive
pressure finally ... much more efficiently ... pushed
a piston to do work. As Cornwall
had tin and copper but no coal ... the Cornish Pumping
Engine design pictured above made the most economical use of coal which
had to transported by ship to the region. This reduced the need for
horses on the surface workings ...
as the same engine technology could also be adapted to work as a
winding engine to
raise people, waste rock, and metal from the mines.
As the 1800s gathered steam ... the operators of textile mills were getting tired of using
waterpower for running larger and more complex spinning machines and looms ... and miners were also
getting a lot better at mining coal ...
Pretty soon, you couldn't go for a
stroll
anywhere in England without burning your arm on the steam engine attached to one of these now 'dark satanic mills'.
The
'Industrial
Evolution' had slowly taken place all around England during the span of
two hundred years. Looking back in the 1880s, an English historian said
the
changes were in fact 'revolutionary' as they had radically changed the
structure and growth of the economy, the nature of 'manu-factory' work,
societal roles and professions, education, and so on ...
The engine pictured above comes from an equipment handbook from 1901.
This particular engine was designed in England for use in a mine in
Chile. These pumps could generally last 50 or 60 years.
Among the wide variety of pumps and winding engines being used at
Cape
Breton coal mines in the early 1900s, there were still a few imported
Cornish
Pumping Engines soldiering on at the older mines ... their genes
tracing back to the time when Cornwall needed to be more energy
efficient.
Back to Top 
Engineering, Scottie here.
So the mines are using
stationary steam engines which use the expansive characteristics of
steam - that is, steam which contains more pressure than everyday
atmospheric pressure. Stationary steam engine boilers alone are kind of dull
when compared to locomotives ... so here is the general layout of the
mechanical engineering heart of a colliery's boilers, steam engine, and related equipment - from above.
The spade symbol
is located in the boiler room. The boiler fireboxes are stoked with
coal
from the spade end ... and the fire boils the water in the water tank
portion of the boiler above the firebox ... producing steam at the very
top of the water tank. The
three boilers exhaust their coal fire smoke to the smoke stack ... doggie.
The heart
is located in the engine room containing the steam throttles, pistons,
valve gear to cycle the pistons back and forth, and any clutches necessary to
connect the big flywheels to the machinery to be operated. The
flywheels smooth out the force of pistons' individual power strokes for more even
running.
With a railway steam locomotive, the heart room parts are on the bottom, the spade room parts sit on top, and the doggie stack rides at the front of all this.
BELOW is one of two 'engines' which are partially illustrated in the heart room above.
It is connected to the winding gear - diamond.
The second similar engine would be connected to the mine's water pump - club.
BELOW is the winding gear - diamond.
The illustrator's back would be to the engine room ...
with the cables above his head being driven by the engine and flywheel illustrated above.
The cables then descend vertically from the winding gear's wheels into the mine shaft.
If you see the coal cars in the foreground ...
you can follow the rails back to the cage in which they were elevated from the mine.
Just to show that the Victorian, Eiffel Tower styling of the usually utilitarian winding gear is an aberration,
below is a hard-headed tabular comparison of different brands of boilers used in coal mining in the late 1800s.
You know ...
sometimes it is interesting ...
just to stare at charts like this for half an hour ...
to see what was 'typical' and what was 'unique' ...
to better understand how different life was back then,
and what the engineers were working to achieve ...
Just kidding!
Back to Top
In the diagram above, you can
see work beginning near the shore using a 'Room and Pillar System'.
Similar to the stylized model mine above with its two furnaces, you can
see the same 'pie graph', but this one shows a single upcast fan shaft and two (we assume) downcast
main shaft divisions.
This mine cannot be arranged like an idealized ground hog
burrow with a front and back door ... as the back door would be deep
under the ocean ... instead, the fresh air from the shore will
have to loop back to the shore as the fan continuously purges the
various gases from the
mine.
You will also notice the notation that the slope of the main seam works
out to a drop of 1 unit vertical for each 12 units horizontal.
A steep
Canadian railway mainline might rarely operate on a 2.2 % grade
... this mine, as its narrow gauge cable-pulled railway follows
the coal strata, will operate on a 8.3 % grade.
Back to Top
Get the most from you mine !
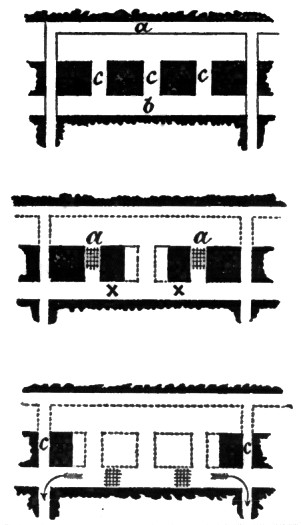
Robbing pillars - seen from above.
The top diagram shows a level which has been mined conventionally with minimal risk.
The cross-hatched areas represent temporary roof supports - wooden cribs filled with rock waste (goaf).
The mine roof support must be maintained as the coal supporting it for millions of years is robbed.
The arrows represent the direction in which to RUN !
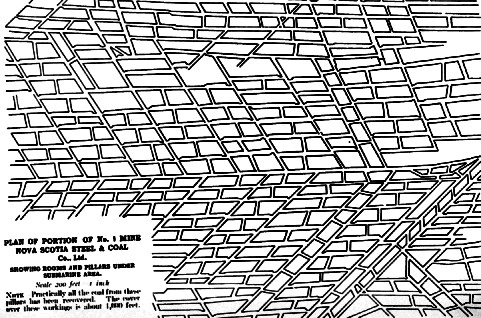
"Plan of Portion of No. 1 Mine
Nova Scotia Steel and Coal Co. Ltd.
Showing rooms and pillars under submarine area.
Note: Practically all the coal from these pillars has been recovered.
The cover over these workings is about 1000 feet."
Pillars could removed more safely (so they said) when a sufficient amount of 'cover' was present.
Until reaching a certain distance from shore with adequate cover ... no pillars could be removed.
Rules for pillar removal were more conservative for submarine areas than when working under dry land.
Back to Top
Boys in the Mines
Not at the 'Bonar Head' colliery
above, but a little farther east at Glace Bay, we see boys in
a mine. Given the low ceiling and the rubble on the track, this may
have been taken in or near one of the rooms where active mining was
taking place. It was generally advised in mining textbooks ... that on
main routes horses or 'pit ponies' should be given adequate headroom to
hold their
necks and heads up naturally. It seems possible that this scene may have been illuminated with photographic flash powder.
"In hauling
the mine cars to the bottom of the slope, the horses are driven by boys
who usually take in four empty cars and bring out the same number of
loaded ones. The horses are kept in stalls cut in the coal stratum near
the foot of the slope. When the boy gets his horse hitched to a trip of
cars, he climbs into the forward car, with lamp attached to the front
of his cap, cracks his whip, and proceeds along the level into the
darkness, shouting or whistling as he feels inclined, to keep up his
courage. If the grade of the mine is not too steep when he reaches the
foot of the first chamber he is to supply, he unfastens the front car
from the others, drives the horse up the incline with it, and leaves it
near the face to get filled; the other empty cars are distributed in
the same way.
"On a siding of the level at the foot of the last chamber visited he
finds a loaded car, to which he hitches his horse and starts on his
return trip to where he started with his empty cars, picking up other
loaded cars on his way to make up his complete rake. If the grade of
the mine is steep, the empty cars are left at the foot of the incline
chambers, and are taken up by the balance power to the working chambers
to be loaded, or filled on the level siding with coal which has been
mined and run down in shutes. At intervals along the main level there
are sidings for this purpose and where rakes going in opposite
directions may pass.
"The position of driver boy in a coal mine is the miner's first step of
advancement. Having entered the mine as a little 'trapper', he
graduates to the advanced position of driver, and afterwards to higher
positions. The term trapper is derived from trap-door, placed as an air
door for the purpose of controlling the ventilating current. At this
door the little trapper must stand or remain like a sentinel from the
time the first rake of cars passes it in the morning until the last
comes out at night. His duty is tiresome and monotonous. He is alone
all day, save when other boys and men pass through his door. His abode
is a hole cut in the rib of the passage, and, as his light is dim and
often goes out, he can do little to amuse himself but whistle. To save
his oil, the little fellow often works in the dark.
"When he hears the sound of a footstep or wagon approaching his door his
duty is to pull on a string, one end of which is attached to the door
and the other secured where he can grasp it in a moment, when the door
will open. After the passengers or cars have safely passed, by slacking
the rope, the door shuts of its own accord. The trapper boy is
generally contemplative and quiet. An observant spectator says of the
little trappers:
'Sitting so long alone in the
darkness the become thoughtful, sober, sometimes melancholy. They go
silently to their homes, when they leave the mine; they do not stop to
play tricks or joke with the fellows; they do not run, nor sing, nor
whistle. Darkness and silence are always depressing, and so much of it
in these young lives cannot help but sadden without sweetening them.' "
Story of the Springhill Disaster, 1891
Glace Bay boy miners.
The lights on their caps look like the whale oil open flame torches.
In 1873, a boy had to be 10 years old to work underground.
In 1891, the age was raised to 12.
After the Great War, children had to be in school until the age of 14
and by 1923 they could not work underground until the age of 16.
In the mining communities, schools often concentrated on preparing youth for a career in mining,
if training went beyond the basic literacy and math of the lower grades.
The effective enforcement of safety and other mining regulations were affected by ...
* The availability and integrity of provincial mine inspectors.
* The company's desire for cheap labour compared to the cost and probability of legal sanctions.
* The financial stresses of large families ... or the desire of boys to begin to do 'a man's work'.
(Sometimes no one objected if a numeral or two was changed on a paper record somewhere)
Springhill, Nova Scotia, February 21, 1891
(among 125 miners killed in an explosion)
Alexander Bunt - 15
Ernest Chandler - 16
Thomas Davis - 15
Joseph Dupee - 12
John Dunn - 13
Roger Ernest - 15
James Johnston - 16
George Martin - 14
David McVey - 16
James McVey - 14
James Pequinot - 15
Peter Reid - 13
Ross Murdoch - 16
Philip Ross - 14
Edward Smith - 14
Douglas Taylor - 16
Back to Top
Endless Rope Haulage & Tippler Work
With this system, standard narrow gauge coal cars were towed by a winding engine once they reached the main gangway.
If mine access was by a shaft, they would be hauled to the shaft, then hoisted in 'cages' to the surface.
If mine access was by a slope, they would be pulled directly out of the mine on rails by the winding engine.
With the system pictured, the return rope comes back on the pulley - top left.
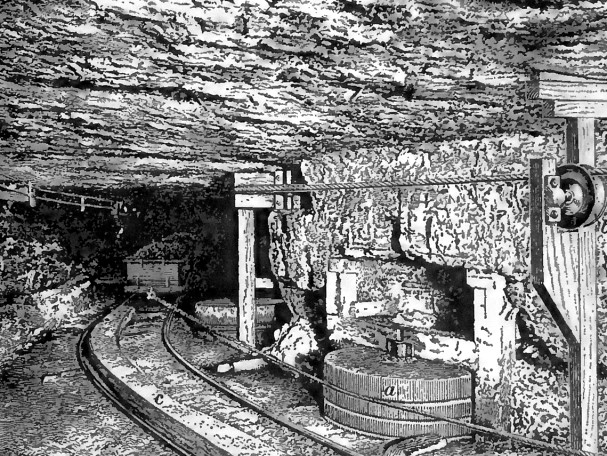
Loaded coal cars would be generally be towed at a walking pace ... in the dark.
With an endless rope system, special patented clips attached to the car would clamp onto the moving rope.
The device at 'a' helps guide the rope around the curve.
With care, ropes could last 2-3 years before replacement was necessary.
Dominion Colliery Number 3, Glace Bay
Data from 1914:
An air compressor provides power for coal cutting and water pumping in the mine.
The mine is 'medium size' for the area - able to produce 500 tons per day.
Underground, 147 men are employed and 46 work on surface.
An endless rope system moves the coal with a total haul 14,000 feet.
Each loaded car holds two tons of coal.
The procession of loaded cars here are headed for :
two rotary tipples with shaking screens and picking belts.
The screening plant is powered by steam engine.
At the left, and centre foreground, regular standard gauge railway equipment carries the marketable coal away.
By the time the Great War
started, modern mines were usually mechanized with modern powered coal
cutting equipment. Unsaleable (small or slaty) slack coal
was essentially waste from the cleaning process. It cost very little to
power everything at the colliery using 'waste coal' fires producing
steam ... to push pistons or spin turbines. In this illustration, it is
not clear how the coal cars are controlled as they travel back down the
ramp to the tipple. It is possible they are re-attached to the endless
rope system which may use the same single rope to haul in both directions.
Traditionally, in the tipple was a company employee to weigh the coal ... and a check-weighman to
verify this weight on behalf of the miners. The miners were paid by the
weight mined per day - a quantity such as that mentioned in the song 'Sixteen Tons'.
A miner's token with their number was attached to each full car sent
from the mine with the weight tallied for that miner ... or split between
two miners working as a pair. The check-weighman was a miner himself, elected by his fellows and paid by them, to ensure they were not cheated on their pay.
The 'tipple' is
where the coal
cars are emptied. Generally, those patented clips attaching the coal
cars to the endless rope ... were released automatically from the
moving rope by a device at the tipple ... the cars were then positioned
and clamped into a rotating cradle ... and tipped over to dump the coal
into the tipple's large hopper. The coal
fell onto shaking screens of two different gauges in this case (see
the flow chart below) ... with screen holes of 2 inches in one, and 3/4
inch in the other. The 'slack' is suitable
for local industrial use to fire a colliery plant or in a nearby steel
mill. Nut coal was a good size for domestic use in home furnaces or stoves. Coal larger
than 2 inches (and much larger) was preferred for locomotive and
steamship use.
The picking belts
at this tipple moved at about 7 inches per second according to the
chart. The slate pickers were young boys, or disabled or elderly miners,
who snatched out loose slate, shale, or coal with impurities as it passed
with the screened coal.
Shale,
slate and other rocky contaminants would not burn and miners might be
docked if their coal was found to be too contaminated by the company
weighman - after all, the company
was paying them for a specific weight of COAL. Hard to see in the the
dark, layers of shale or slate would often adhere to the layers of coal
taken from the ceiling or the floor below, or just get mixed in ...
with blasting or coal
cutting operations.
In steam locomotives (for example) shale or slate would clog the fire
grates at the bottom of the firebox ... through which combustion air
had to move freely. Assuming they hadn't caused a failure on the road
... at the end of the locomotive's trip, the rocky contaminants would
have to be manually removed if they were too big to be dropped clear
when raking the fire and 'shaking the grates' to remove accumulated 'dead ash'.
Boy slate pickers at a US colliery
' [slate picker] boys are artists in their line, being able to spear slate or bony coal with either hand,
and without lifting their eyes, place either in its proper chute. '
Boys were employed in this manner at Cape Breton.
Eventually, their work was eliminated by automated equipment.
This schematic diagram depicts a similar system to that detailed in the flow diagram above.
The screens are being shaken through eccentrics powered by a steam engine.
Back to Top
Technology in Nova Scotia Mines
... and the nature of the industry
Since the mid-1800s, coal mining in Canada required a significant investment of capital and expertise.
Costs, skills, and requirements included:
- Determining the extent and value of the deposit ;
- Legal incorporation and acquiring a mining lease ;
- 'Placing' the shares or debt issued by the corporation ;
- Purchasing appropriate mining equipment and constructing the colliery ;
- Hiring professional, trade and unskilled labour ;
- Preparation of the coal for market ;
- Operation of transportation systems to the customer or negotiating transportation contracts ;
- Political
relationship management (obtaining government GIFTS ... e.g. land,
labour conflict 'resolution', 'bounty hunting', managing international
trade ... (depending on the
circumstances) ;
- Marketing the coal to customers.
Initially, it was generally British capitalists who saw potential
in some of British North America's coal resources. Canada had the
advantage of importing experts and maturing British technology such as
steam
engines and mining equipment for the first coal mines in Nova Scotia
and New Brunswick. Early photographs of Nova Scotia mines show
scenes similar to classic British 'industrial revolution' landscapes -
Newcastle mining cars and sturdy formal brick colliery buildings.
With the completion of the CPR et al, interior western Canadian coal resources - now
having access to a bulk transportation system - were developed. Prior
to this, Vancouver Island coal had been handy for British
Admiralty bunkering.
Coal is a bulk commodity which is most economically consumed locally
... but
passing ships are very 'local'. Again, the British Admiralty was a
customer at Sydney and Halifax as coal grew in importance for warships
over sail. Some astute British captains on the Atlantic noted their
tactical advantage against potential American rivals by insisting on
low-smoking coal when bunkering in Nova Scotia. They figured it gave
them an extra 5
mile advantage as the ship itself (not its black smoke plume) had to be
spotted by an adversary.
As the century turned to 1900, it was more often American capitalists
who came calling ... but there was excellent anthracite in Pennsylvania
and coal almost everywhere 'down there' ... why Cape Breton?
Bounty hunting. The Canadian government thought it might be good to
develop a stronger domestic steel industry and was willing to pay to
help set one up. It is unclear, with perfect hindsight, whether Cape
Breton steel was ever worth all the various costs at the time ... and the environmental price which is still
being paid. Canada would always remain a coal and steel pygmy compared
to Britain, the US, and European countries strategically ramping up
their industrial and military strength ... Yo! Wilhelm !
... However, around 1900 ...
memories
were still fresh of Van Horne bringing in massive quantities of steel
rails
from England and the US to meet the CPR's demands. More
transcontinental railways were being built and the prairies were
already being
weighed down by a virtual web of steel. If the Century was to belong to
Canada, Canada should have a strong domestic steel industry producing rails
and for domestic manufacturing (e.g. farm equipment and railway rolling
stock) ... so the wisdom
went.
Looking back, we were at least proud and valued steel producers during the
World Wars when every little bit was needed ... well ... you know ... a lot of
our proud Canadian steel ended up as rusty scrap as fast as we could produce it - either on the
battlefields of Europe or sometimes at the bottom of the Atlantic.
Considering technology ... Beginning sometime around 1900, the great demand for coal to power virtually everything,
and the proximity of American mining equipment suppliers, resulted
in a great variety of coal mining technology being present in the coal
mines of Cape Breton. Much of the durable British influence was still to be
found. However, for modern internationally financed collieries,
American equipment was often chosen.
Old ... 'British':
- Horses;
- Boy labour for trapping, driving and slate picking;
- Picks and black powder to free the coal;
- Steam engines on the surface for hoisting, ventilation and pumping.
New ... 'American':
- Powerful compressed air equipment for coal cutting, water pumping, and even compressed air locomotive hauling in gassy mines;
- or ... Electrical equipment for naturally-wet low-dust low-gas mines ... or a mix of compressed air, electricity and steam;
- Air and electricity conduits efficiently carried energy right to the coal face or the location where the work was done;
- Large centralized steam turbogenerators produced electricity for multiple collieries;
- Specially designed equipment to prepare the coal for market ... eliminated manual picking belts and other labour-intensive tasks;
- Air ventilation fans and water pumps of efficient advanced design improved both safety and productivity.
- The ability to swap
mine 'waste', flammable gases, heat, steam, electricity ... back and forth
between coal mines and steel mills improved profitability.
A modern compressed air driven coal cutting machine circa 1900-1910.
The undercut coal could be shaken off the ceiling with some of the newer explosives.
Hand picks would still be used in older, more cramped collieries during this period in Cape Breton.
Finally ...
If we consider human resource management practices to be a 'technology' ...
Companies imported other 'technologies' to Nova Scotia adapted from some American coal mining companies ...
- The Nova Scotia Steel and Coal Co; and the Dominion Coal Co used the traditional 'company store' system of pay stub check-offs
... which minimized the disposable income and independence of miners
living in isolated colliery communities. A 1942 stub included deduction space for:
supplies, rent, coal, trucking, check-weighman, doctor, benefit
society, church, hospital.
- The British
Empire Steel Corporation, Ltd., Montreal ... beginning in 1920 ...
consolidated the assets of the companies above, along with the Dominion
Iron and Steel Company so there was only one major employer of coal miners in the province.
- The company practice of firing and blacklisting
any man ... throughout the coal mines and steel mills of the entire
province ... if he was deemed to be supporting any co-ordinated action
against the employer - including any efforts to 'organize' for a union.
- The ability to evict the blacklisted man's family from company housing without notice during any season.
- The use by the company of para-military forces ( e.g. " Pinkerton's
" ) and the state's military forces 'to protect company property' during lockouts or strikes.
'Glace Bay during the June 1909 strike'
Source: "The Company Store: J.B. McLachlan and the Cape Breton Coal Miners 1900-1925"
John Mellor, 1983 & The Miners' Museum Glace Bay
Back to Top
Some Uses of Coal in the Early 1900s
New coal shipping pier, North Sydney
Nova Scotia Steel and Coal Company
circa 1900
Although the photo resolution is poor, you can see a few coal cars on the pier.
The pier design allows for loading both
steamships bound for the St. Lawrence or the Atlantic
and sailing ships for coal delivery along the coast.
1898 Brochure
Before electricity became available for street lighting, town gas, locally produced by processing bituminous coal, was used.
Natural gas for home use was generally not available until after World
War 2. The pipeline infrastructure for moving and storing natural gas
in regional salt cavern 'hubs' for high winter demand had not yet been
developed.
"LaSalle Coke Company (in 1944)...
on the south bank of the Lachine Canal in the town of LaSalle, just
outside the city limits of Montreal, covering more than one hundred
acres ... All gas distributed in the Montreal district for household
and industrial use is manufactured at this plant."
You can see a 'coal boat' by a tall unloading crane at the left edge of the photo.
At the top of the photograph, you can see two of the frames holding the
expandable gas reservoirs - they look like large oil tanks in cages.
Essentially, this gas has hydrogen, methane, ethylene, carbon monoxide
and other good stuff which burns. Other chemical by-products are
produced such as coal tar and ammonia. Coke, almost pure carbon which
burns like barbecue charcoal, is left after all the volatile gas has
been 'cooked off' the bituminous coal. Coke could be used in stoves and
was sometimes used by steam locomotives in urban areas with strict
bylaws limiting smoke production.
1898 Brochure - CPR's represented, eh?
In one reference, a suggestion was made regarding why
coal operations of DOMCO were never as profitable as they might have
been. Whitney from Boston was the capitalist who organized the various
'Dominion'-named enterprises on Cape Breton which will be covered in
other pages. It was suggested that much of Dominion's coal output was
locked into low-priced contracts with Whitney's New England Gas and
Coke Company with major operations in Boston.
Back to Top 
Glace Bay
"One of Dominion Coal Co. Ltd. Collieries, Glace Bay, Cape Breton, Nova Scotia"
A CNR photo published as a postcard by C&G MacLeod Ltd of Sydney.
Probably circa 1955.
Of course this is the tipple ... and you'll note the coal which has been graded and loaded is larger than 'nut' size.
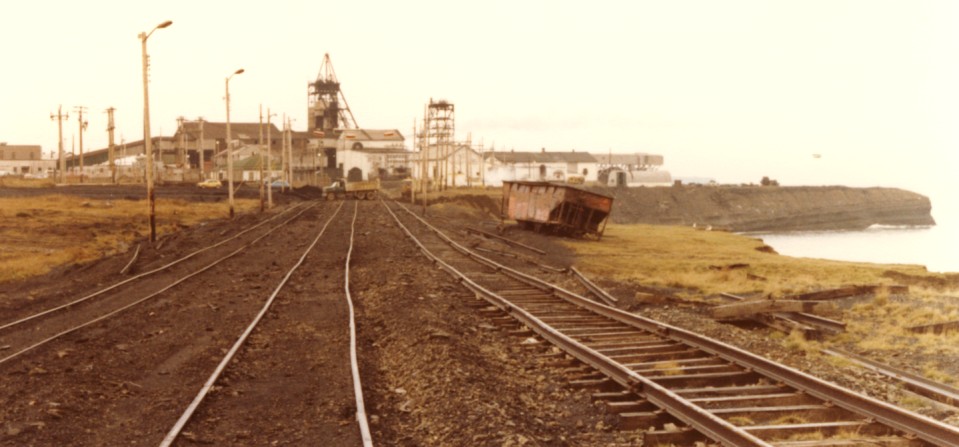
The Glace Bay colliery scene as recorded during our vacation in 1980.
Back to sitemap